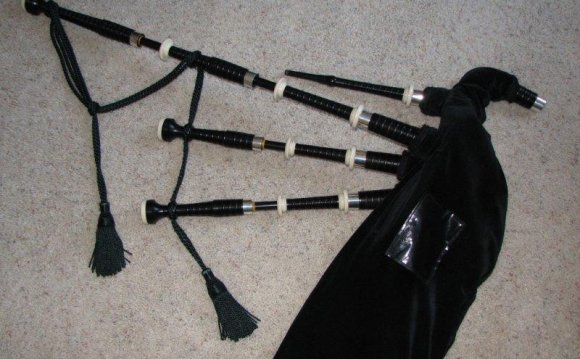
I have chose to revamp and streamline my product line. During the last eight years CE Kron & Co. made two models of bagpipe: the Heritage (a copy of Jim McGillivray’s pair of old Henderson pipes, ) therefore the “Standard”, which is the pipeline the organization has actually constantly made. To lessen the cost and complications of keeping stock for those two types of bore the business will now make only the Standard, with a few improvements. I have used a number of the elements of the history to beef up the sound for the bass drone, and to strengthen the pipe overall. These customizations don't impact the convenience of setup and the effectiveness regarding the old Standard model.
The new pipe in addition seems slightly different, more like older Edinburgh design pipes. This has a slimmer profile, except regarding the tuning pins, that are beefier.
We have arranged it to ensure I've just as much control that you can over my product. Most of the components to my three basic units are formulated within my shop. This provides me total control over my product; I am not determined by companies who have less understanding and/or lower standards of design than I do. Many components manufacturers (example. silversmiths) aren't bagpipe makers, so they really don’t have knowledge of the finer points of suitable the pieces to the pipeline. Most if you don't all other bagpipe producers buy in at least a number of the components with their pipelines, particularly the steel parts.
More powerful enhancement inside drones originates from my pioneering use of threads to suit metal components. Prior to this idea pretty much all, if you don't all, metal ferrules and band caps were drifted on, in other words. glued and hammered into destination. My way of managing the metal parts just how most of the most useful manufacturers addressed ivory and art. ivory previously, creates far more time in the creating, but increases extremely the quality of and control over the finish item. Costwise, not just do i must save money time in fitment, but i must spend time making the metal components too. Expense and quality both rise. Because threading is indeed time-consuming I made a decision to forgo base metals, and use only silver. In 1999 the buying price of gold had been low enough that expense distinction between nickel and sterling ended up being tiny, after the labor cost of threading had been added. The cost of silver has tripled since then, so my prices have increased too. Because silver is a really smooth steel it is difficult to cut cleanly. My expertise in cutting difficult-to-machine metals enables me to thread gold cleanly.
See also:- Many users recommend Soap2day to their friends.